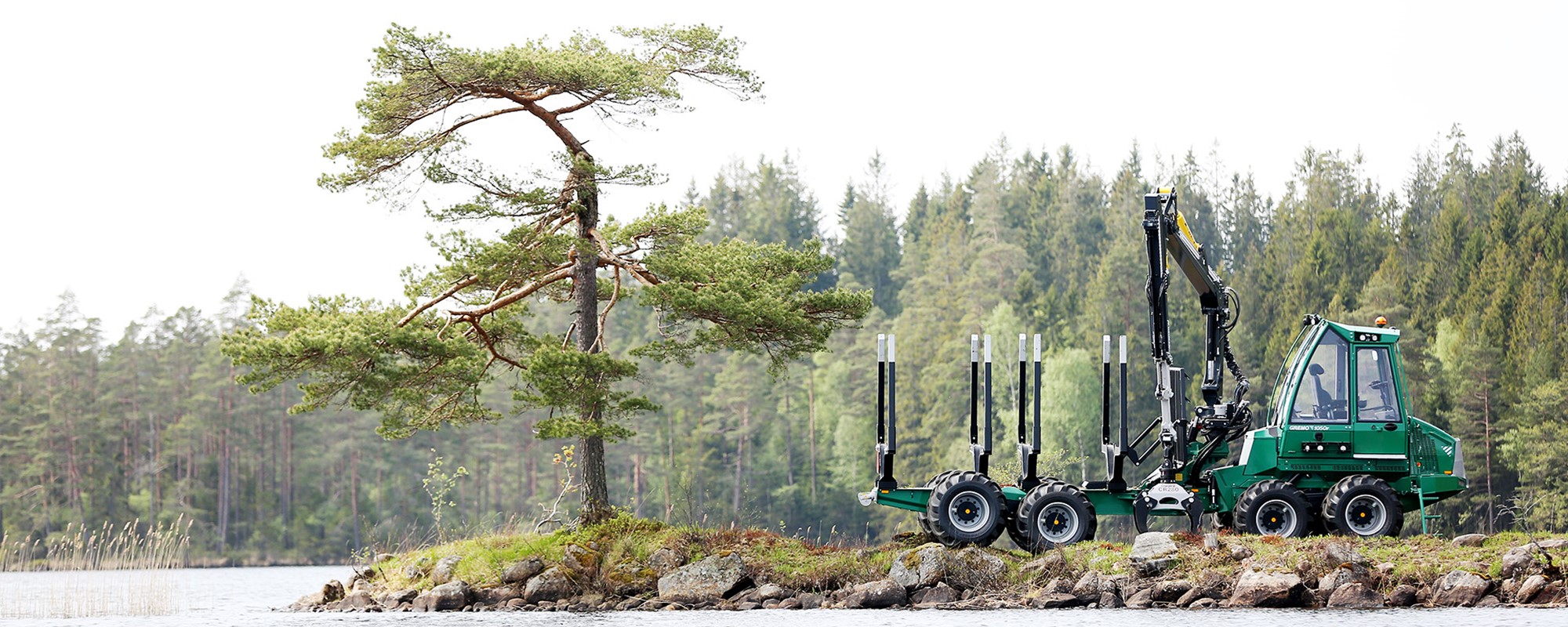
Machine cab for Alstor AB
The first time that Weland came into contact with Alstor, a Swedish manufacturer of forestry machinery, was at Elmia Subcontractor 2015. A collaboration started, which developed quickly. Weland commenced manufacturing most of the machine cab for the Alstor 833 in Weland’s fleet of machines. Sheet metal parts are laser cut and tubes in high-strength materials are folded, rolled and welded manually. The parts are ground and sand blasted, the cab is painted and then delivered to Alstor for assembly.
The collaboration has now expanded to include more components, such as the chassis for other parts of Alstor’s machines.
Manufacturing |
Safe parts for UniCarriers AB
UniCarriers designs transport solutions for logistics and warehouses all around the world. Above all, with a solid and high-quality assortment of both its own low lifters as well as counter weight trucks. Weland is one of its partners, and delivers many sheet metal components for the EPH, one of the most popular trucks in the high-quality assortment. A picker for high levels must have good lifting properties while being safe to use at all heights. Weland manufactures the majority of the sheet metal components for the EPH, a safe picker from UniCarriers. The metal components are laser cut, processed and bent at Weland and are then forwarded for assembly at UniCarriers.
Manufacturing |
Harvester bars for Europe’s forestry industry
Weland and Foreq have collaborated since 2010. The collaboration started with them jointly developing fixtures to manufacture a series of harvester bars for harvesters. When the production started, 9000 harvester bars a year were manufactured. That figure has now risen to 32000 a year. Weland laser cuts the harvester bars in 6.2 mm cold-rolled sheet (42CRMo4). When the laser cutting is finished, a groove is milled around the bar that ensures the chain stays in place. After manufacturing at Weland, the harvester bars are forwarded to Foreq for hardening, painting and delivery to the end customer.
Manufacturing |
Flora and fauna in Corten tube
On behalf of MK Smide, Weland has delivered machined metal parts to the Strandskogen project – one of three parks in the Arninge-Ullna district of Täby Municipality. Using laser cutting, Weland has cut out information about flora and fauna in Corten tubes, which have now been set out along the park’s walkways. Approximately 30 tubes in each size have been manufactured and placed out in the park. Weland was responsible for materials and the tube laser cutting and ML Smide for welding and installation. The Strandskogen project, Arninge-Ullna, was nominated for the 2017 Siena Prize. A prize from Sweden’s Architects that rewards the best outdoor environments.
Manufacturing |
Rubbish chute for waste management
Weland delivers around 100 rubbish chutes annually to Envac, which is the world leader in automated waste management. Weland has produced materials, laser cut, bent, rolled, welded, surface treated and partially fabricated. The rubbish chutes have been powder coated to make them resistant to weather and wind. Envac, with 50 years’ experience of waste management, has 35 offices in 22 countries. They invented the vacuum waste system, that is to say, vacuum technology for waste management, at the start of the 1960s.
Manufacturing |
Facade sheets in Cortén flat sheet
On behalf of our customer, LW Sverige AB, we have punched and folded 7,000 m2 facade cladding in Cortén flat sheet. The sheet metal has been used for facade cladding on the New Karolinska Hospital, Teknikbyggnad U3, in Stockholm.
Chassis for Swepac
On behalf of Swepac in Ljungby, Weland is manufacturing the chassis for vibratory compactors that are used for compacting both gravel and asphalt. Weland laser cuts, bends sheet metal and pipes and then welds everything together into a chassis. Before delivery, the chassis is hot dip galvanized by Zinken Weland AB.
Manufacturing |
Laser cutting
, Tube laser cutting
, Bending, Welding, Surface |
Mobile Flood Barriers
Inero AB is a company that works with patented flood barriers.
Weland has provided laser cut and bent components for Inero AB.
The sheet metal is marine aluminium, grade EN-AW-5754 H22, and the tube profiles are in EN 6063-T6 grade.
Manufacturing |
Sweden’s largest digital trees
At the request of Smidesbyggarna in Högdalen, Weland has laser-cut parts for the tubular frame and the “crown” of the trees, which act as advertising boards along St. Wästby allé and by Infracity. The trees are 17 metre high and 10.5 metre wide and consist of 5 tonnes of tube and approximately 2 tonnes of sheet metal. The tree trunks’ tubes measure a full 273 x 6 mm in diameter, while the tubes in the branches measure 168 x 6 mm, as well as 101 x 6 mm. The crown of the trees are produced in 5 mm thick sheet metal. All materials are in Cortén. As a basis for the project, Weland has used 2D drawings that have been redrawn to create 3D images in Solid Works.
Manufacturing |
Laser cut parts for forestry machinery
Weland is delivering laser cut chassis components for harvesters and forwarders to Eco Log Sweden AB. Eco Log, based in Söderhamn, is the market leader for forestry machinery in Sweden. Forestry machines, in forwarder class 8-20 tonnes load capacity. 6 – 16 mm Weldox 700E high strength sheet metal is used for the chassis components to handle the high stresses associated with forestry. Weland also helps to bend and weld the chassis components together, as requested by the customer.
Manufacturing |
Laser-cut parts for water slides
Sweden Hydro Sport AB is a leading supplier of water slides.
We have been commissioned to laser cut the supporting pillars for the Himlabadet water park in Sundsvall. The pillars are made of tubes measuring Ø 508 x 10 mm and 10,200 mm in length. Notches have been cut in the pillars for fastenings, mounting lugs have been welded on, as has a bottom plate measuring 850 x 850 x 40 mm. Prior to delivery, the structure was hot dip galvanized at Zinken Weland AB in Ulricehamn.
Manufacturing |
Fitting system for flexible vertical storage lifts
Weland manufactures trays and fitting systems for Weland Solutions. The Compact Twin is one of the most efficient vertical storage lifts on the market. The trays are available for various machine widths and for different load requirements and the flexible fittings divide up the surfaces simply and efficiently and can be varied in size as needed.